作業効率が高まる
「倉庫レイアウト」
の基本
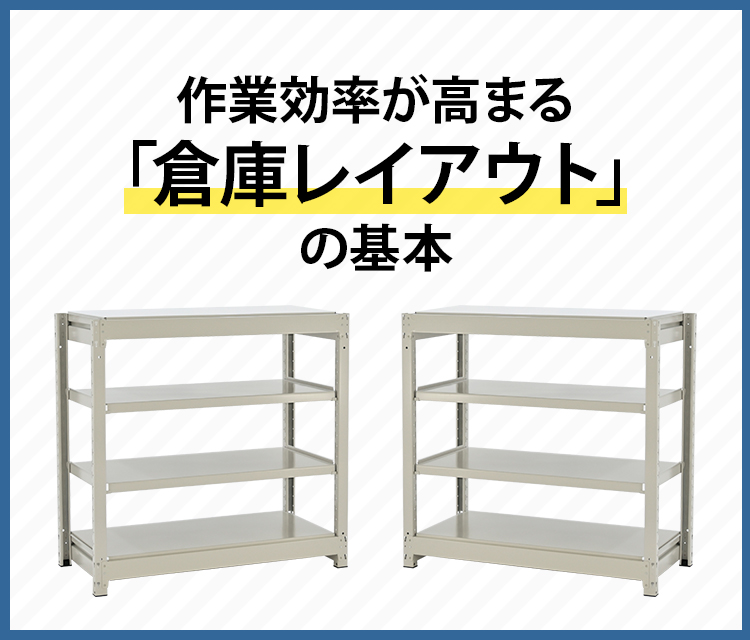
動線から考える倉庫レイアウト
収納力を重視しすぎたレイアウトは注意が必要
スチールラックのレイアウトを考える際に限られた空間の中で、いかに収納容量を増やすかという点ばかりが重要視されることが多いですが、収納力重視の倉庫レイアウトは作業効率を低下させる要因となりやすく注意が必要です。
入荷から出荷までの作業を確認
作業効率の良い倉庫レイアウトを考えるためには、まず倉庫内でどのような作業が行われるのかを確認し、どの程度の作業スペースが必要なのか、スペースを共有するべき作業と分けるべき作業はどれなのかなどを考えます。
多くの倉庫・物流センターの作業工程では、入荷(荷受)、保管、移動、ピッキング、仕分け、梱包、出荷、棚卸などがありますが、今回は「入荷→入荷検品→ピッキング→出荷検品→出荷」のシンプルな作業工程とします。
一筆書きができるスペース配置が理想の動線
入荷から出荷までの作業工程を作業順で一筆書きの動線を作ります。実際の現場では、作業スペースを広く確保することや、一筆書きの動線を作ることは難しいこともありますが、保管スペースと作業スペースのバランスが重要
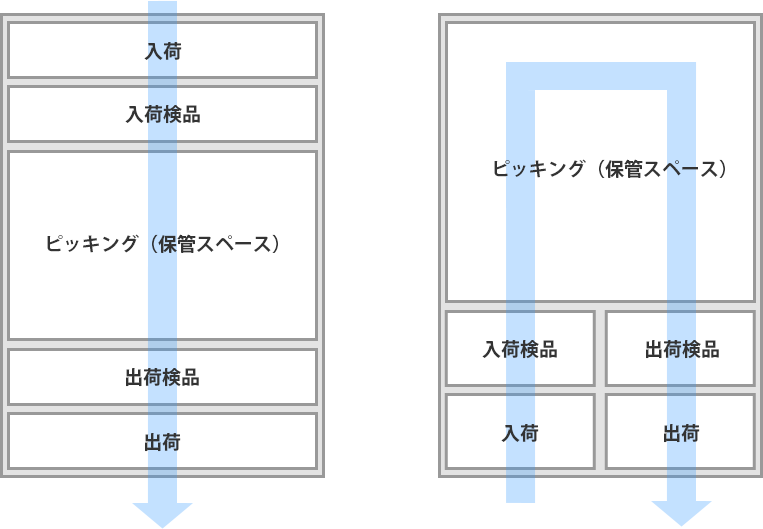
出庫頻度による商品グループ分け
効率の良し悪しは移動距離に表れる
倉庫内の効率の良し悪しは、倉庫で働く従業員の「移動距離」に表れます。効率の悪い倉庫ほど、引き返したり、遠回りするような非効率な動きが増え、必然的に移動距離が長くなります。反対に効率の良い倉庫では、無駄な移動が減り、移動距離が短くなります。
出庫頻度によるグループ分けで移動経路をコントロールする
倉庫内での移動の多くはピッキング時に発生します。どの商品をどこのスチールラックで保管するのかによって移動経路が決まるため、倉庫効率化とは、商品の保管配置の最適化とも言えます。
商品の保管配置の最適化は、まず商品を「出庫頻度」にてグループ分けします。グループ分けは「ジャンル」や「仕入れ先」といったカテゴリー分けされていることが多いと思いますが、効率化という観点からすると「出庫頻度」で分けることが効果的です。
Aグループ商品 | 流動性・出庫頻度が高い。作業効率を優先する |
Bグループ商品 | 流動性・出庫頻度が平均的。作業効率と保管効率の両方が必要 |
Cグループ商品 | 流動性・出庫頻度が低い。保管効率を優先する |
より多くアクセスする必要があるAグループ商品の配置を、出入り口付近に集中させたり、入り口から出口への最短距離の動線付近に集中して配置することで、倉庫内での移動距離の短縮がなされ、ピッキング効率が上がります。
倉庫レイアウト例
出庫頻度別の基本の商品配置レイアウト
入口と出口に近いエリアに出庫頻度の高いAグループを配置し、奥の方にCグループを配置することにより、長い移動を必要とせずにピッキングを完了できる割合が増えます。

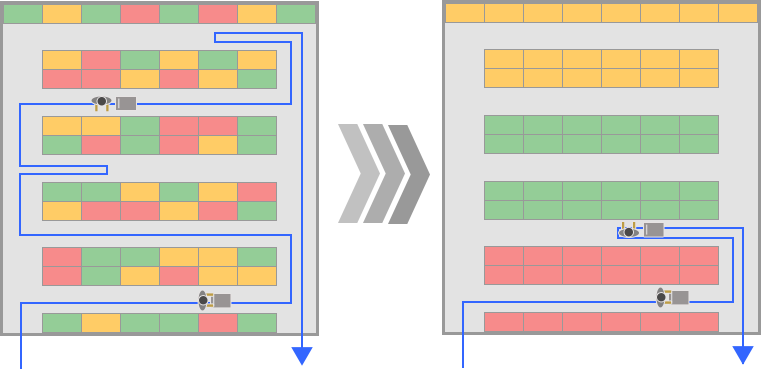
Aグループを出口への最短距離の通路に集中させる
入口と出口が離れている場合、入口から出口までの最短距離の通路にAグループの商品を集中させるだけでも、移動距離の削減が可能です。
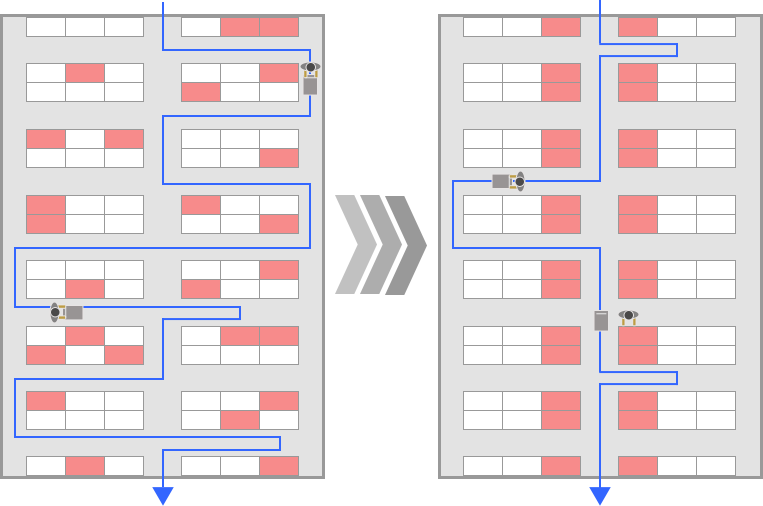
Cグループは作業効率ではなく収納力を優先する
作業効率を下げずに収納容量を増やしたい場合は、Cグループに着目します。出庫頻度の低いCグループは、作業効率ではなく収納容量を優先したレイアウトでも倉庫全体の作業効率を低下させにくいからです。台車の通れない通路幅に設定し、スチールラックを増やして設置することも検討してみてはどうでしょうか。
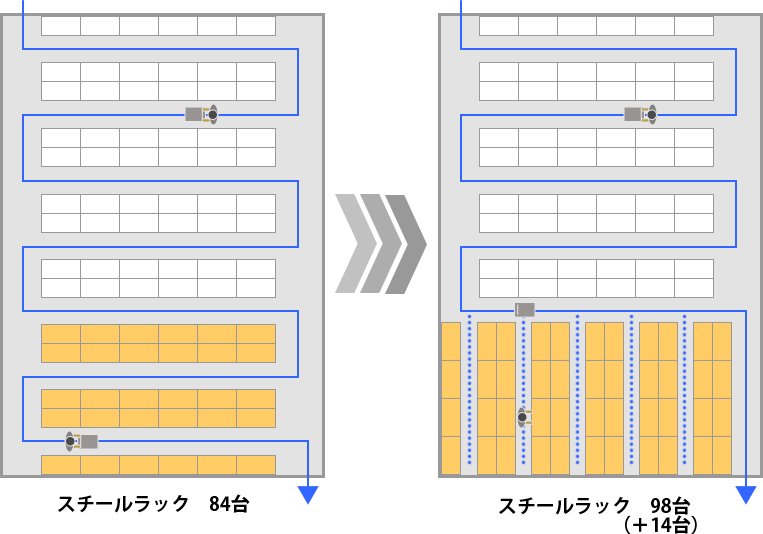
移動棚を組み合わせて収納容量をアップする
移動棚を組み合わせたレイアウトです。Bグループを棚を移動棚に、Cグループはその移動棚の奥のアクセスのしにくいスペースに配置。アクセスのしにくさはありますが、変更前のレイアウトに配置されていたスチールラック16台中11台はこれまで通りアクセスしやすい配置のため、作業効率を下げることなく、大幅な収納容量アップが見込まれます。
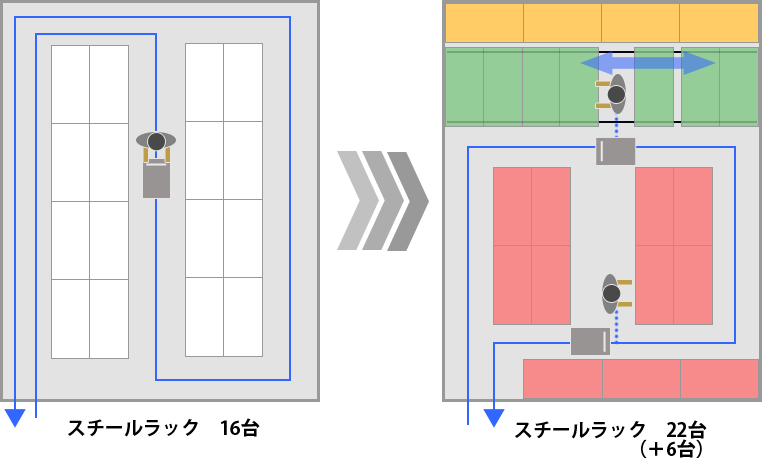
実際の倉庫では、様々な条件の中でレイアウトを考えなくてはいけないため、例のようなレイアウトを組むことは難しいかもしれませんが、出庫頻度によるランク分け、移動距離、通路幅を最適化し作業しやすく収納力のある倉庫レイアウトを考えてみてください。